The production of coated paper or coated board requires contactless drying of the coating which is applied until it is suffiently dry to touch guiding rolls or drying cylinders. This is done either in Offline Coating Machine or in Online coating sections.
Our drying solutions are customized to your specific process needs and available energy sources, including the use of
- gas infrared drying (GemDryer®)
- electrical infrared drying (DryMaster™)
- the combination of infrared drying with air drying (UniDryer®)
- air drying (FoilMaster™, TurnBooster™, AirBarDryer™)
- air cooling (CoolMaster™)
The most common layout is to start with infrared drying after the coat application, immediately followed by air dryers. The combination of infrared drying and air drying provides a perfect combination of available technologies to optimize your drying system for optimal quality and energy efficiency.
For most graphical coatings, it is crucial to start the drying with a high drying rate to reduce risk of binder migration and mottling, while controlling the temperature and avoiding overdrying or overheating the coating components. We have a long experience in designing coat drying in such a way that the coated board or paper surface keeps optimal print quality when used by your customers.
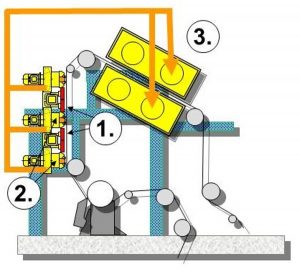
Concept for optimal coat drying with 3 high efficiency products: high performance gas IR emitters GemE (1), integrated air drying with UniDryer® (2) concept and ERS (3) : exhaust air from IR is used as energy source in Air Dryer.
For specialty coatings and barrier applications, the combination of infrared and air drying within the same dryer, allows for optimal temperature control along the drying to ensure the delicate surface coating remains perfectly stable without risk of blistering or other coating defects linked to wrong drying strategy.
We supply every non-contact drying equipment which is required in your coating process, including the web cooler if paper or board temperature needs to be reduced before winding it on the pope.
Whether your project is a new investment, an upgrade or a rebuild, we can offer a solution which considers the total drying strategy, including the simulation of the cylinder drying and optimizes your overall coating operations.
Our products are designed for optimal energy efficiency, high reliability, long lifetime and flexibility.
Contact us :
paper@ircon-solaronics.com
UniDryer®
The best of gas infrared & air drying in one dryer
READ MORE >
DryMaster™
The combined eletrical IR & airfoil dryer with temperature actuator
READ MORE >
FoilMaster™
The effective air dryer with optimal uniform drying
READ MORE >
GemDryer®
The gas IR dryer with highest power density
READ MORE >
TurnBooster™
The compact combined air dryer & air turn combination
READ MORE >
AirBarDryer™
The compact solution to add air drying with limited investment using exhaust energy from IR dryers
READ MORE >
CoolMaster™ Float
The solution to cool the web with chilled air or ambient air before the reel
READ MORE >